Generally, when injection moulding is performed, a finished and ready-to-use or assemble part with other components is obtained.
However, there are several opportunities to further improve the aesthetic and functional performance of injection-moulded parts through various surface treatments.
Often, our clients rely on our industry knowledge to understand which surface treatment is most suitable for their product, both from a functional and aesthetic point of view, but also from an economic standpoint.
So, let’s see what the main post-processing options are.
Let’s take a look at them together:
1.Printing on plastic and labeling;
5.Chromium plating or metallization;
Now let’s delve into each of these methodologies in more detail.
There are different reasons for deciding to print on a plastic product. Often, you want to add a label or add instructions to the surface of the part. The main methods of printing on plastic are:
- Heat printing
- Pad printing
Screen printing
Labeling
When performing heat printing, a film with a glossy metallic coating is used. The film is pressed onto the plastic surface using a hot stamp, allowing it to adhere to the surface.
When performing pad printing, a soft silicone pad is first pressed against a metal plate (pad printing cliche) on which a slight engraving, previously filled with ink, bearing the image and/or text to be printed on the part, and then pressed onto the plastic product surface, from which it releases the decoration.
Screen printing can be used predominantly on flat surfaces and is often used when the required decoration is too large to be achieved through pad printing. A stencil bearing the printing pattern and an ink-impregnated mesh are used so that the stencil is reproduced on the mesh. When the mesh is pressed onto the plastic surface, the color is transferred to the part, obtaining the print.
Finally, the application of adhesive labels allows further customization of the plastic surface.
This technique allows graphics or textures to be integrated directly into the mould, resulting in a decoration that is inseparably linked to the moulded part. The result is a high-quality aesthetic finish that is wear-resistant. In this case, the film is positioned in the mould during its creation. This method makes it possible to produce very beautiful and refined parts from an aesthetic point of view.
Lasers allow logos, codes or inscriptions to be engraved directly onto the surface of the part, without the use of inks or adhesives. It is a very precise and durable technique, and a recent invention.
The application of paints, enamels or coatings allows obtaining glossy, matte or metallic effects, to enhance the aesthetic appearance of the products. In addition to conferring an attractive appearance, painting can also perform important practical functions, such as protection from UV rays and weathering or strengthening of surfaces to improve scratch resistance.
These treatments give the plastic part a shiny and metallic finish, providing a prestigious appearance. This method serves to increase the aesthetic value of the injection-moulded part and gives the impression that the product was made with metal. The most suitable thermoplastic material for chromium plating is ABS, but even more technical polymers such as polyamide or polyester can undergo this type of finish.
Chromium plating and metallization also protect the plastic from UV rays or heat sources. Finally, coating the plastic with metal can also serve as a shield against electromagnetic fields.
Which solution to choose? The choice depends a lot on the aesthetic and functional goals you want to achieve for your product. We also recommend visiting this page of our website to further explore the post-moulding services offered by CSplast.
Don’t hesitate to contact us to evaluate together the best post-processing options for your plastic components!
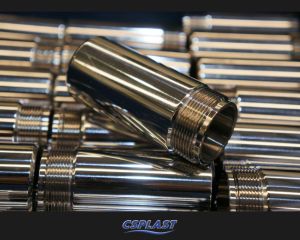